How Toyota's 100-year textile history influenced FCV hydrogen fuel cell car
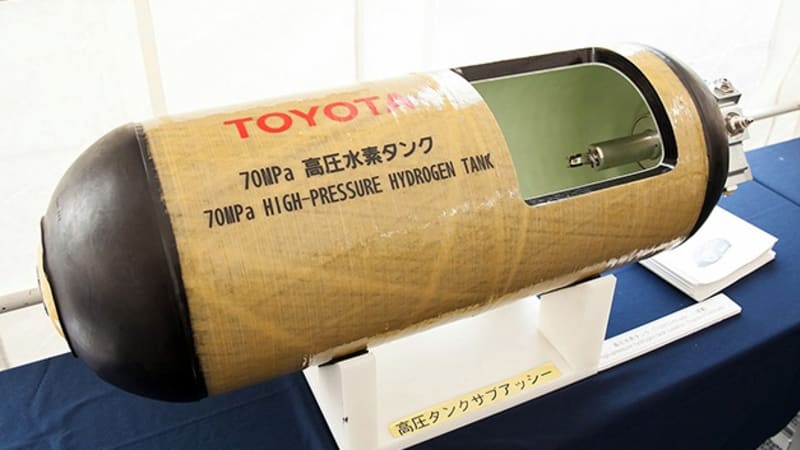
Turns out, Toyota had a surprising ace in the hole when it came to building the new fuel tanks for the FCV hydrogen fuel cell car, which is coming next year. Well before Toyota became the Toyota Motor Company, it was the Toyota Industries Corporation and it made textile looms. This is important because the main structure of the hydrogen tank is wound carbon fiber. When Toyota set out to increase the strength of the tanks to hold hydrogen stored at 10,000 psi (up from 5,000 in the previous tanks), it was able to draw on its 100-year-old history as it designed its car of the future.
"A lot of that textile experience came back when we did the tank wrapping." - Justin Ward
"We have a lot of experience with textiles," Justin Ward told AutoblogGreen at the 21st World Congress on Intelligent Transport Systems (ITS) in Detroit this week, "and a lot of that textile experience came back when we did the tank wrapping." On top of being able to hold the higher-pressure hydrogen, Toyota's first attempt to build its own hydrogen tank was six times faster than the industry standard, so it saved time and money as well as working better. The company will also be able to inspect its own tanks. Ward is the general manager of powertrain system control at the Toyota Technical Center and hydrogen vehicles are something he knows a lot about.The reason for the stronger, 10,000-psi tanks is because the 5,000-psi tanks only offered around 180-200 miles of range, even with four tanks in the early $129,000 FCHV Highlander hydrogen prototypes. The FCV only has two, but they will able to deliver the 300-mile range that customers told Toyota they wanted. Dropping the number of tanks not only obviously reduced the cost for the tanks themselves but also the number of valves and hoses and other components you need.
Despite the benefits of higher compression, going much higher doesn't make sense. 10,000 psi is the "natural progression," Ward said, because "you start to bump up against compression inefficiencies." Think of an air compressor. When hydrogen is produced at a wastewater treatment plant or a reforming site, Ward said, is it at around ambient pressure (14 psi). That has to be raised, using compressors, all the way to 10,000 psi. "That takes energy," Ward said, "and every doubling of pressure adds another doubling of energy needed, so it starts to add up pretty fast if you go too high." Component specifications are also fine at 10,00 psi, but more difficult at higher levels.
"Current regulations require pressurized vessels to be visually inspected every" few years.
Toyota's hydrogen tanks also have an important sacrificial abrasion layer on the outside, which is going to be important when the tanks get into the hands of everyday drivers. While you can apparently safely shoot a bullet at the tank, "current regulations require pressurized vessels to be visually inspected every so many years," Ward said. "Depending on the country you're in, it could be two or five." The inspectors will be looking for any evidence of an impact and, if found, the tank would need to be recertified or replaced. "You'd have to hit a rock or something" to damage that abrasion layer, which is designed to make abrasions or dents easy to see, Ward said.Ward said that exactly who would do these inspections (the Toyota dealer or a certified inspector, similar to how smog checks are done in some states today) has not yet been decided in the US, but he did say that, "in the US, it's not enforced so well, so the inspection would most likely be done at the Toyota dealer." In Japan, it's likely to be done at a federal agency Featured GalleryToyota hydrogen fuel cell prototype
Source